Paul Friday’s industrial relic – a Moto Guzzi Nuovo Falcone – produces a lot less power than it could. In this series of features from the RC RChive, he embarks upon a quest to make the old banger sizzle…
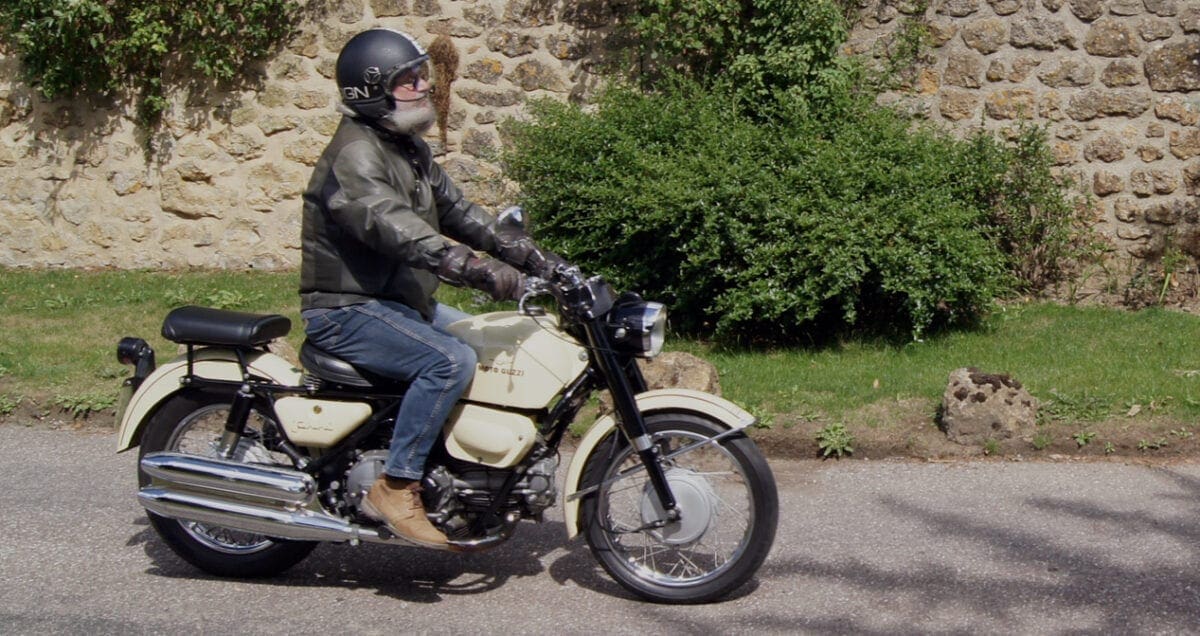
Here’s Editor Westworth aboard one he owned a few years ago…
My bike makes a lot less power than it could. While we all accept that old bangers make up for it in charm, there are some improvements that could be made that would not detract from its blessings. I want to make it clear though, right from the outset, that this is not a go-faster tuning guide. There are plenty of people who can wring more power out of old metal. If that is what you want, then talk to the madmen who race them.
What this is about is making the engine more usable and more efficient. I want to squeeze every erg out of that petrol, not only to annoy the Treasury and the oil producers, but also those pious folk in their two-ton diesels who pontificate about how they get 100mpg while sat in the dry listening to the stereo.
My poor old bike was designed and built back when God was still an apprentice. It was good for its day, but the understanding of ‘good’ has moved on a bit since then. I want to use some of that knowledge to make my dinosaur dance. Like most old bikes, mine has barely adequate ignition and a poor combustion chamber shape. These and the valvegear are the main areas that can be improved. The advantage of changing these is that most of the work is invisible and will save fuel and engine wear.
The ignition on my bike is better than a lot of old timers, as it’s a first-kick starter and it still works in the rain. Thankfully it’s a battery and coil system, which makes it much easier to live with than a magneto. Don’t get me wrong, magnetos are fine for aero engines, which are basically fixed revs. They don’t work well where engine flexibility or easy starting is important, though. The points and coil set-up would be fine, but it’s all getting a bit old and worn out.
The main problem is the auto-advance. This was the best the designer could do at the time, and it provided a straight-line advance that approximated to what the engine needed, for as long as it was in good condition. Sloppy moving parts and weak springs have made it easier these days to time the ignition at full advance and just put up with the lumpy tickover.
The other issue is the cylinder head. A lot of the problems here can be laid at the door of the designer. The engine is a big single with large valves, so it’s difficult to get a proper compression ratio at the same time as efficient combustion.
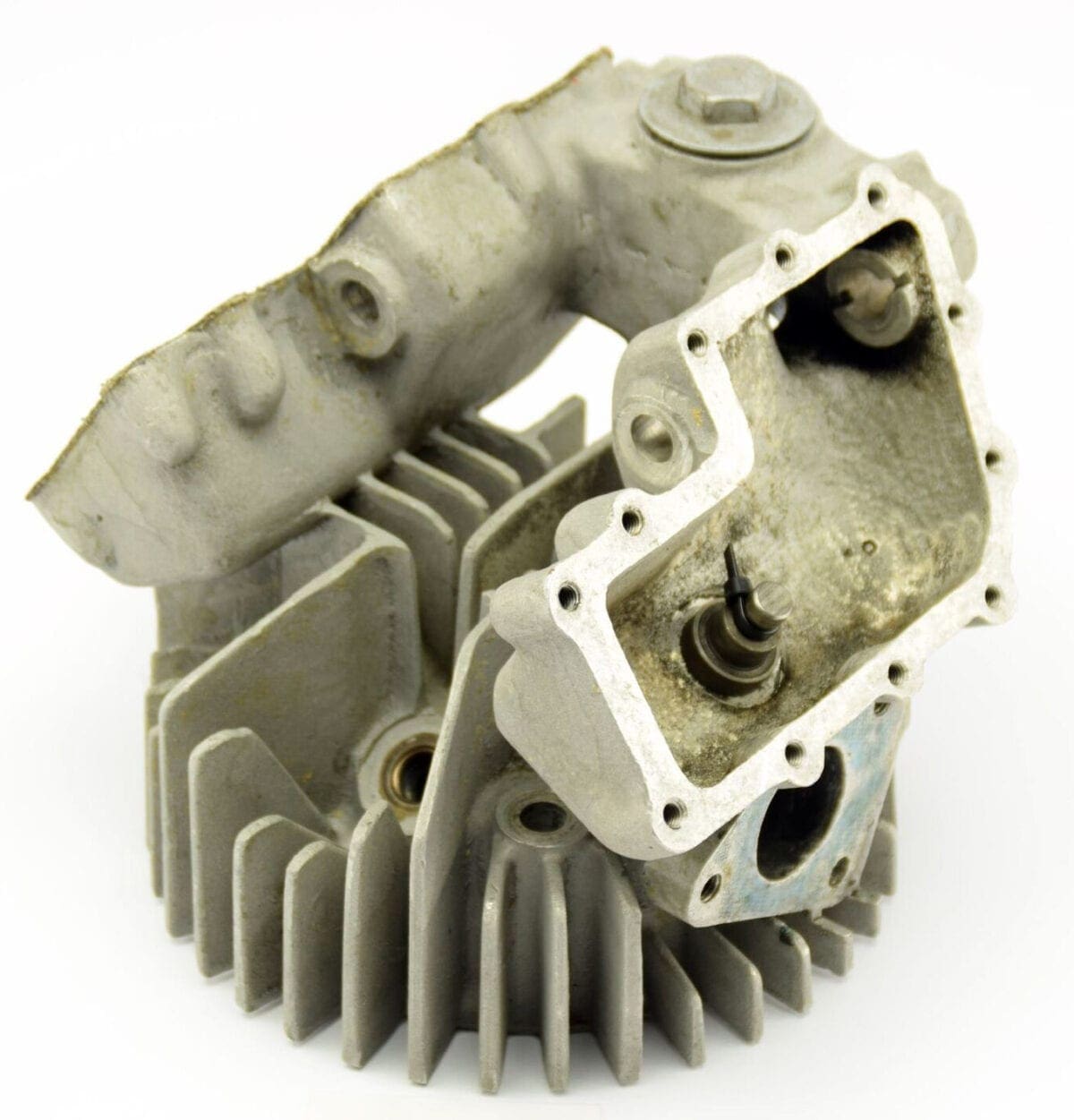
Imagine you were an engine designer back in the early days. You want good gas flow, so you assume you need big valves. You will only be using two valves in the head, as multi-valve designs are complex and troublesome. To get the biggest valves you can fit in the head, you set them at large angles to the axis of the bore. The included angle between the valve stems will be quite large, between 60° and 90°. There isn’t sufficient space between the valve heads to get the spark plug in the centre of the cylinder head, so you set it off to one side.
This also means you have plenty of room to run the pushrods up the other side of the head. The dinner plate sized heads of these big valves run the risk of hitting each other, so you have to be careful with the cam timings. They also risk hitting the piston, so you will design some cutaways in the piston crown. Those big valves are also heavy. Their inertia means that you can’t push them open and closed as quickly as you would like. You need big springs to control them, and you have to start them moving early to get them open in time, without over-stressing the valve gear. This is why Ducati invented their desmodromic valve gear – to be able to move big valves around quickly without having to use massive springs.

The end result of these design compromises is a wide-open hemispherical combustion chamber with a couple of big valves crammed into the roof. The only way to get the compression ratio up is to use a domed piston. Getting it to clear the valves is an art. The best you can do is something like the Manx Norton engine or the Moto Guzzi Le Mans; everything is big and strong and working hard to stay out of its own way.
You know that engine efficiency increases with the compression ratio, but pushing this design results in a combustion chamber shaped like the skin of half an orange. It takes an age for the flame front to burn across such a thin and highly-quenched space, so a huge ignition advance is needed. Even if you leave the compression ratio down in single figures, it still takes an age for the flame front to burn across the wide open space. Whatever you do, you still need a large ignition advance.
When it comes time for your regular bench-racing down at the pub, try comparing the maximum ignition advance of everyone’s engines. The most efficient design is the one with the least advance. My old relic needs 44°, which makes it a sad old duffer. In comparison, the worst I could find was a BSA B34 running 9:1 compression, and that needed 40·5°. Other values I have found for more modern machinery are:
Yamaha XT400 35° at 6000rpm
Yamaha XT550 35° at 6000rpm
Yamaha XT600 36° at 4500rpm
And as an aside, any rocket-jockey that fits an after-market ignition advancer to make his plastic fantastic go faster will get the same effect much cheaper by pursing his lips and making engine noises. The manufacturers go to great lengths (these days) to get the best possible combustion. Advancing the ignition alone is pointless. modifying the engine so that it needs a greater advance is probably a big step backwards.
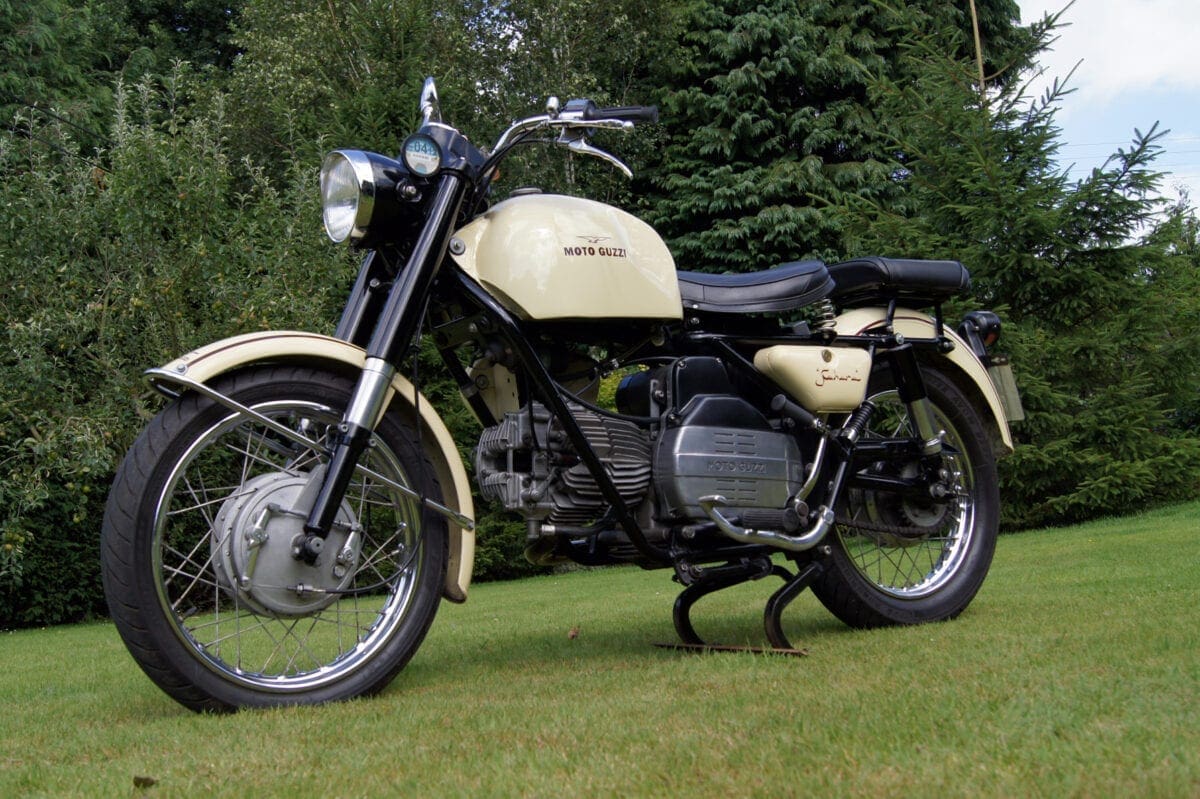
Compared to the traditional big chamber / big valves approach, modern engine design has followed a different path. Using a pair of small valves for each inlet or exhaust actually provides more gas-flow area at lower lift, than a single larger valve. It’s easier to fit four valves in a cylinder head than two, so the total gas-flow area can be made significantly larger. The smaller valves can also be placed with a smaller included angle between the stems, allowing the combustion space to be smaller. Another advantage is that the smaller valves have more seat area in ratio to their size than big ones. This means they run cooler, so can stand higher compression ratios.
The spark plug also fits neatly into the top of the head between the valves, and the area between them can be shaped to provide squish. Because the mixture burns so quickly, much less ignition advance is needed. This means that the rising piston is compressing the mixture, not struggling to compress a burning and expanding fireball. The result is high compression ratios without pinking, small ignition advances, good gas flow and excellent efficiency.
But this about the bike I own, not the one I would buy if I was sensible.
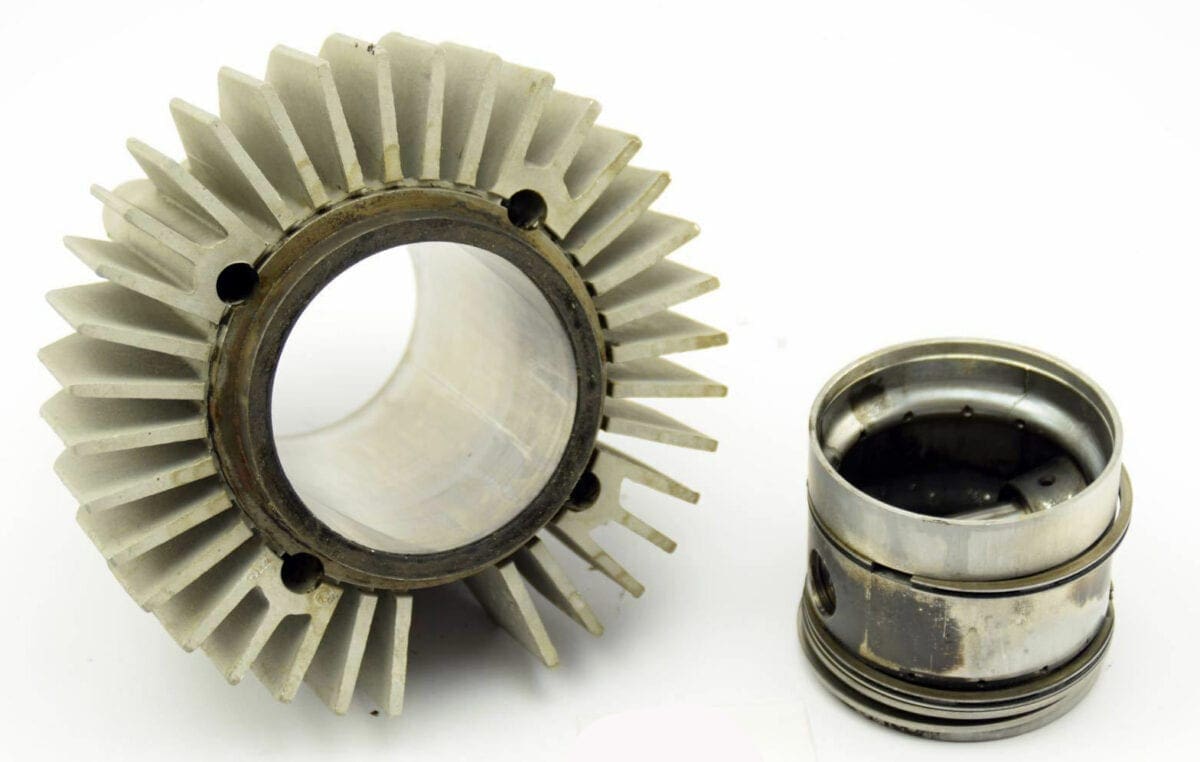
My bike is no Manx. It has a flat-topped piston with a couple of small scoops to miss the edges of the valves and a pimple in the middle as a nod to efficiency. The compression ratio is 6·85:1, which is pretty pathetic. The valves are huge – 47mm inlet and 40mm exhaust with 10mm diameter stems. Each valve needs a pair of big springs to keep it in contact with the camshaft. All that mass thrashing about can’t be good for accurate valve timing or even the life of the engine.
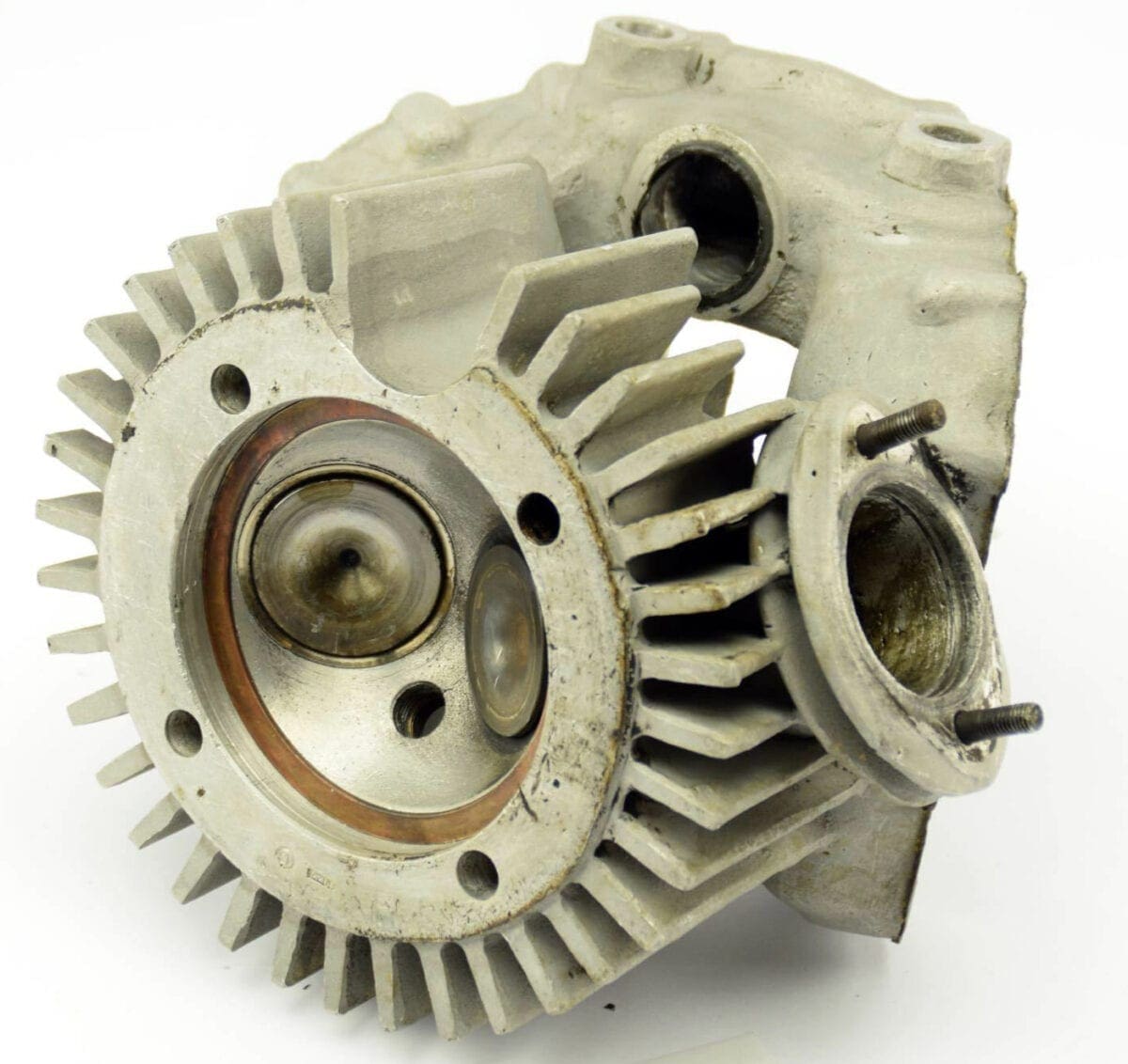
For comparison, look at the 400cc engine used in Suzuki’s off-roader DR-Z. The bore is 90mm, making it comparable to the Guzzi’s 88mm. Into the head they have squeezed two 36mm intake and two 29mm exhaust valves with an included angle of 28 degrees. It manages an 11·3:1 compression ratio and puts out 40bhp. This is no highly-strung screamer either, but a solid mud-puppy that has to be able to plonk and pull at any revs and in any gear.
This makes my bike sound pathetic, but it is only old. Almost all old bikes will have the same problems, because they were designed from the same assumptions. This means that anything I do to my bike you could do to yours. My Grand Plan is to improve the whole ignition process, and to do it in stages so that I can learn what is happening. I intend to change the points and bobweights for a box of clever electronics and get a spark so big it will light coal. I also intend to improve the combustion chamber shape and raise the compression ratio, while reducing the stresses on the valve gear. The end result should be almost invisible, except for a discrete extra length of HT lead.
What I am after is not a higher top speed, although a tad more would be handy on the motorway. No, what I want is better acceleration and the ability to hold speed against a headwind or incline. If I am really smart, I could improve (or at least not worsen) the fuel consumption at the same time. My regular commute is a couple of miles of A road, thirty miles of motorway, another couple of miles of A road and a mile in town traffic. The bike spends most of its time at full throttle, slipstreaming lorries. It gets between 45 and 50 mpg, depending on the weather and my urgency. I’m sure I can do better.
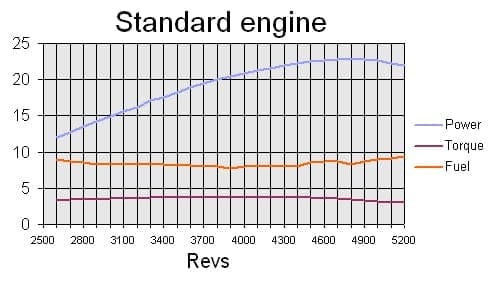
Standard curves for a New Falcon. Bit of a flat torque curve!
So this will be the quest: a better engine with a touch more oomph. Except reality always has a way of poking its finger in your eye. Take a look at the graph of numbers for the standard engine. It makes a throbbing 26·2bhp at 4800rpm. On standard gearing that corresponds to about 80mph. Maximum torque is hard to place, as the curve is so flat. I’m guessing that it’s around 3·8Kgm at 3800rpm. That would be around 65ph, which is why it’s so hard to go any faster than that. The best fuel consumption is at 3900rpm. You would expect the engine to be most efficient at maximum torque, so that makes sense. You can see that this is no road-burner. My sums give it a BMEP figure of 142psi, where a good target is perhaps 200. They also give it a thermal efficiency of 0·25, which is depressing. Plenty of room for improvement! For comparison, the Suzuki DR-Z 400 mentioned about has a thermal efficiency around 0·30 and a BMEP of more than 250.
The first and easiest step would be to replace the whole mess of points and bobweights with an electronic set-up. ‘Set and forget’ the adverts promise. If only it was so simple, but that huge 44 degree advance gets in the way as it seems to be beyond the reach of commercial systems. There is hope, however (light at the end of the spark plug?). I wondered if it might be possible to adapt a system from a different engine, or even to build my own. What I want is an electronic box to do the advancing of the spark, and a second box of tricks to make fat sparks at the plug. If I could get both sets of tricks in the same box, I would be a happy man.
So the Grand Plan is first to replace and match the existing ignition timing with an electronic system. Then I will get the cylinder head improved. Finally, I will tweak the ignition advance curve to match the improved head. Tune in next episode to see what happens…
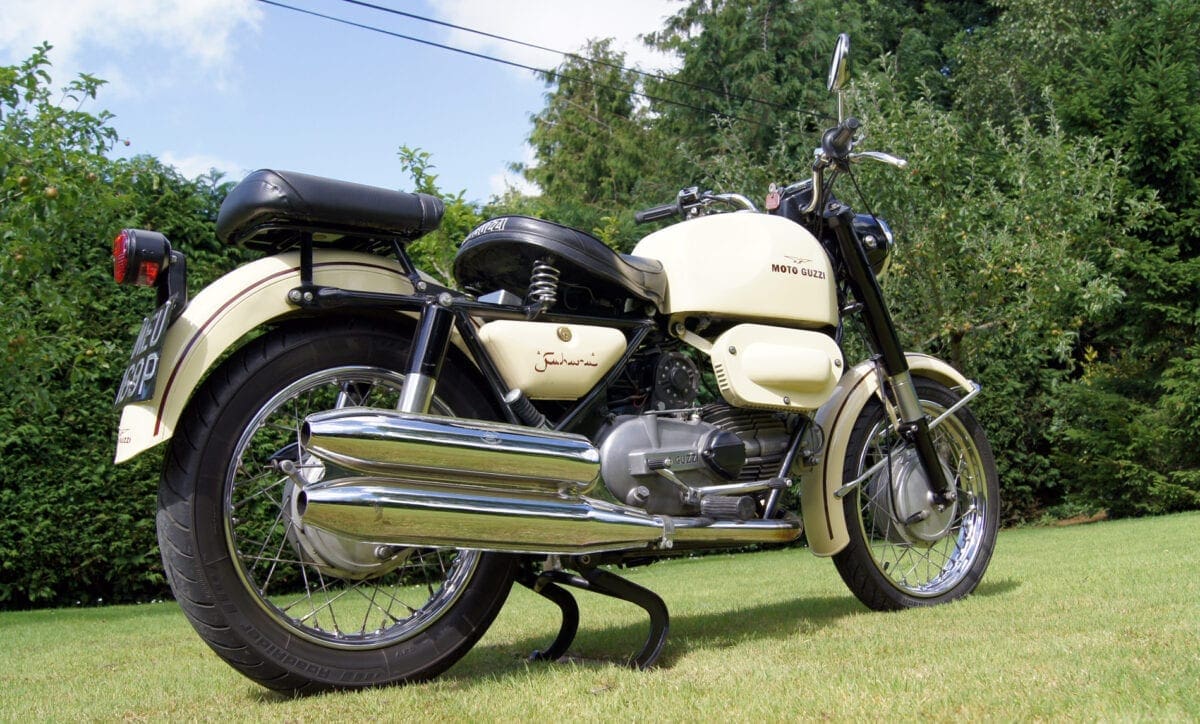
——-
This feature originally appeared on the old RealClassic website. It’s been slightly updated with new illustrations to suit our current incarnation
We’ve featured Guzzi’s Falcone several times in the magazine. So if you want to read more features about this motorcycle, you’ll find it in these issues: May 2017 / RC157 and May 2016: RC145 and Feb 2015 / RC130. All are available as digital downloads or as print magazines delivered to your door
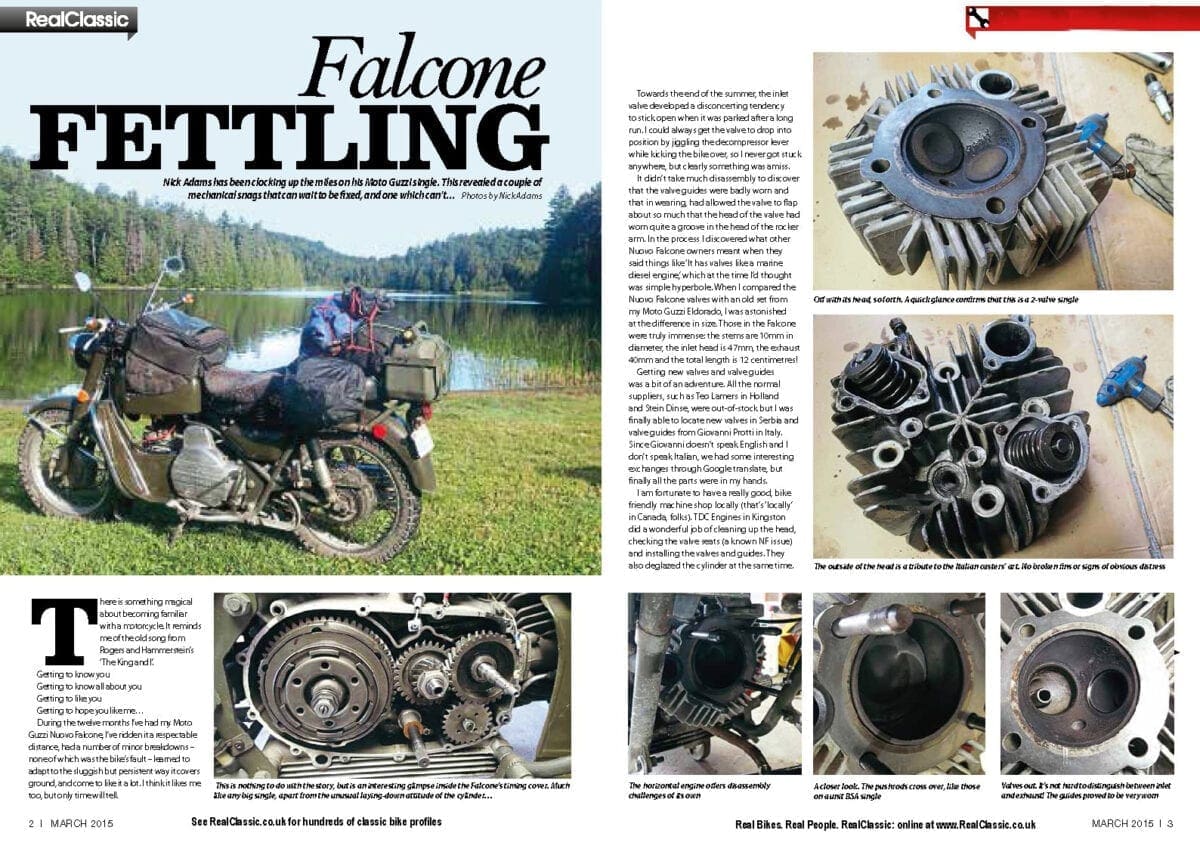
——–
Words: Paul Friday / Images: RC RChive